This UK newsprint mill is a recycled newsprint mill which underwent an upgrade in 2003.
SPIRAC supplied an equipment train to provide fine and coarse rejects screening, classifying, dewatering, compaction, transport and outloading. Equipment includes SPIROGUARD (Channel Screen), SPIROSEP Duo (for separation of floating and settling solids from the reject screen), SPIROPAC (dewaterer and spiral compactor) and high volume outloading shaftless conveyors (U620).
SPIROGUARD® Channel Screen SPIRODRAIN
Effluent passes through the SPIROGUARD® CS500 screen via the plant’s open canal. A 5mm perforated screen collects solids which are removed and transported by a spiral with a nylon brush along its periphery.
Flowrate = 100 lps with 3% DS, 0.5% fibre content
The SPIRODRAINTM/conveyor receives reject material (plastic, wires, etc.) from the drum pulper hopper above, as well as from the CS. The drain deck allows drainage of free water.
Capacity = 15 BDt/d at 10-20%DS, results in approx. 6.5m3/hr
SPIROPAC® dewaterer/compactor
A U620 transport conveyor fitted with a pneumatic slidegate discharges the drained rejects into either the SPIROPAC® dewaterer (normal operation) or bypassing it into the outloading conveyor. The SPIROPAC® unit compacts and dewaters the reject material. The drain screen is 8mm perforated plate. Compression doors are automatically regulated to provide optimum and controlled dewatering.
Inlet: Approx 15% DS
Outlet: Approx 30% DS depending on material composition
7.5 kW motor / 15 RPM gear drive
Requires intermittent flushing water connection, 25 l/m, 2min per 30 min; compressed air at <5 bar.
SPIROSEPTM DUO420
Screened rejects fluid is fed from the screens above into the top of the SPIROSEP unit. The fluid impinges on a damper plate to break its momentum and reduce turbulence. Spray nozzles and a paddle assembly (not shown in this view) encourage fibre and light density particulate to flow toward the screening conveyor where solids are captured and transported out.
Denser solids settle to the bottom of the classifier chamber and are extracted gradually via slowly rotating screw conveyor. Fluid, free of particulate is discharged via a v-notch overflow of weir.
Capacity = 18 lps
Maximum TSS = 1%
Maximum fibre content 0.5%
Let us contact you
Products
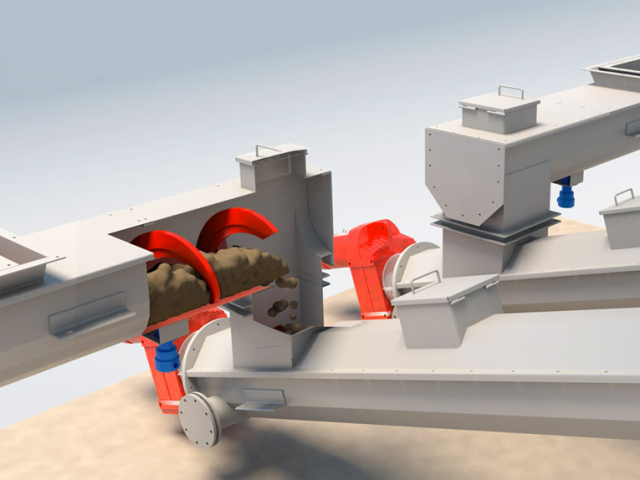
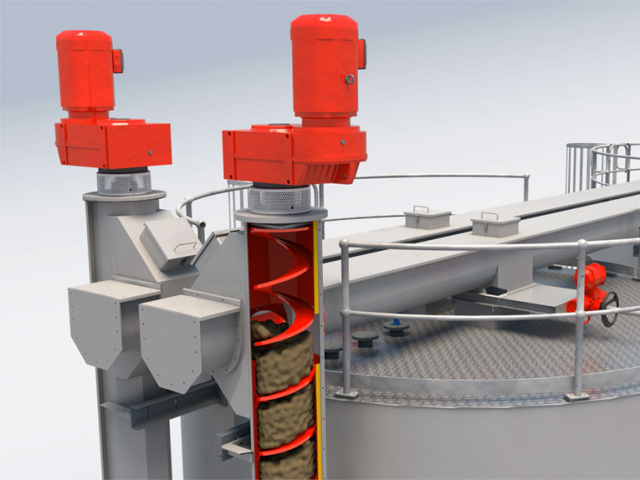