- Shaftless Spiral Conveyors
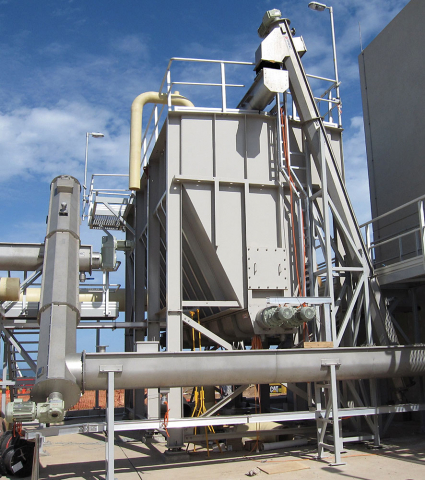
The market is filled with different solids handling systems (also known commonly as wastewater material handling solutions), and understandably there are a number of differences between them.
This article will compare shaftless screw conveyors with the other options on the market, including cake pumps, conveyor belts and shafted screws.
Cake pumps
Cake pumps are seen as the solution for those instances where pumping through vertical sections of pipe is necessary, but there are draw backs.
Reliability: Cake pumps are unreliable, and the costs of operation increase with sludge dryness. Shaftless spiral conveyors are reliable across a range of moisture content.
Cost: Cake pump parts are expensive, and the cost to rebuild is often high. Shaftless spiral conveyors have a long service life and low maintenance costs.
Design and maintenance: Cake pumps run the risk of foreign objects causing catastrophic failures, even with small items, while shaftless spiral conveyors feature an open design and high torque to allow the passage of objects up to 90 per cent of trough diameter.
Cake pumps also use polymer or water injection rings, which are expensive to buy and maintain, whereas shaftless spiral conveyors only have one moving part.
There is also the risk of sludge quality being adversely affected from inlet through to discharge with cake pumps, while shaftless spiral conveyors largely maintain sludge quality.
Operation: Cake pumps cannot be run dry, while shaftless spiral conveyors can.
Conveyor belts
Similar to their counterparts in the mining and industrial sectors, conveyor belts in solids handling carry out much of the same functionality - moving material from an inlet to another location. There are reasons why this approach isn't ideal for solids handling.
Reliability: Conveyor belts have a short life expectancy as a result of the system complexity. Shaftless spiral conveyors can be expected to last 20-25 years.
Cost: Conveyor belts feature a number of moving parts, which in turn means maintenance is frequent. Shaftless spiral conveyors, on the other hand, feature just one moving part.
Design and maintenance: Workers require access across the length of a conveyor belt to carry out maintenance, while shaftless spiral conveyors require such little maintenance as to render the issue of access moot.
Operation: With conveyor belts, material is liable to stick to the belt and fall off from the bottom side. With shaftless spiral conveyors, the system is fully contained, meaning there's no spillage. Conveyor belts are also difficult to fully enclosure in order to block odours, while shaftless spiral conveyors are closed by design, with neoprene lid seals and a single odour port.
Shafted screws
Shafted screw conveyors use rotating helical screw blades in the same way as shaftless spiral conveyors, but the design raises some issues.
Reliability: Bearing lubrication is a serious maintenance problem with shafted screws, while shaftless spiral conveyors feature no bearings. Auto-lube systems are also prone to breaking down, resulting in bearing seizures.
Cost: As shafted screws have low fill rates that require large trough cross sections for equivalent transport capacity, they're not the most cost-effective option. Shaftless spiral conveyors have less than half of the cross-sectional area for equal capacity.
Design and maintenance: Gritty sludge will erode the trough bottom of a shafted screw and spiral flights, while shaftless spiral conveyors feature sacrificial liners that can easily be replaced.
Operation: Screenings can wrap around the shaft, creating a tangled mess that's difficult to unwind. Shaftless spiral conveyors have no shaft for the screenings to wrap around.
Speak to SPIRAC
To learn more about shaftless spiral conveyors, including why they're a better choice than the other options on the market, get in touch with SPIRAC to learn more.