- Asia Pacific News
- Europe News
- North America News
- Shaftless Spiral Conveyors
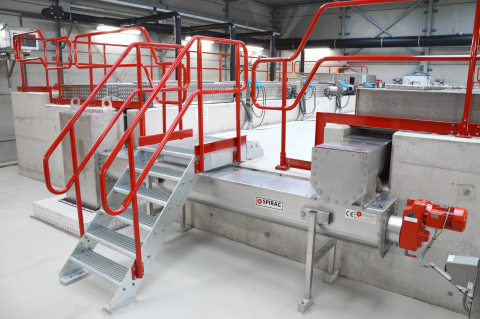
When comparing shafted conveyors to shaftless spiral (screw) conveyors, it becomes evident that the latter offers a distinct set of benefits for material handling.
The traditional shafted conveyor design incorporates a central shaft supported by hanger bearings, with a rotating screw attached to it. This structure provides stability and rigidity to the conveyor system. In contrast, the shaftless spiral (screw) conveyor operates without a central shaft. Instead, it features a spiral-shaped screw running inside a trough. This design proves particularly advantageous when handling sticky, viscous, or irregularly shaped materials that could lead to blockages or entanglement in a shafted conveyor.
Shafted conveyors excel in transporting a range of bulk materials, including dry powders, granular substances, and small to medium-sized solids. However, shaftless spiral conveyors shine when managing challenging materials prone to wrapping or adhering to a traditional screw. This includes sludge, wet and sticky substances, fibrous materials, and large irregularly shaped objects. The smooth inner surface of the shaftless spiral ensures reliable conveying without the risk of blockages. Additionally, the absence of a central shaft allows shaftless spiral conveyors to achieve higher fill rates.
In terms of maintenance and cleaning, shafted conveyors generally demand more attention due to the presence of a central shaft, hanger bearings, and seals. These components necessitate regular lubrication, alignment, and inspection for wear and tear. Cleaning can be challenging, especially when dealing with materials that tend to stick or accumulate. On the other hand, shaftless screw conveyors offer simpler maintenance and cleaning procedures. Maintenance requirements are reduced with no central shaft and fewer parts to maintain or replace. Moreover, the absence of shaft-mounted hanger bearings minimizes the risk of material build-up, simplifying cleaning operations.
Flexibility and installation options are additional considerations. Shafted conveyors are less adaptable, requiring precision alignment and proper support for the central shaft and hanger bearings. They are often customized to fit specific layouts and may have limitations in accommodating changing process requirements. Conversely, shaftless spiral (screw) conveyors offer greater installation flexibility. Their design allows for variations in inclination angles and configurations, making them easier to integrate into existing systems or adapt to evolving operational needs.
In summary, the choice between a shafted conveyor and a shaftless spiral (screw) conveyor depends on material characteristics, handling requirements, fill rates, maintenance considerations, and installation flexibility. While shafted conveyors are suitable for general bulk material handling, Shaftless spiral conveyors provide advantages when dealing with challenging and sticky materials and simplified maintenance and adaptable installations.