- Asia Pacific News
- Europe News
- Municipal Solutions
- North America News
- Shaftless Spiral Conveyors
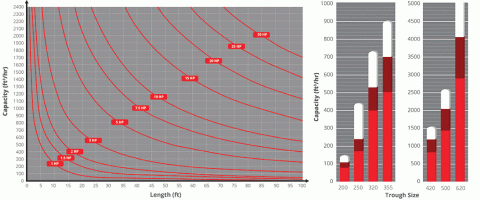
When designing a sludge conveyor system, a combination of factors need to be considered when sizing the trough, spiral and drive motor/gearbox:
- Conveyed material characteristics
- Trough Size, length and design
- Spiral diameter, pitch and model
- Motor power and gearbox RPM
- Elevation angle of the conveyor
- Feed method
The overriding consideration is how to minimize wear and capital cost thereby ensuring the lowest cost over the life of the whole system.
Wear rates are determined by the conveyed material characteristics, drive speed, spiral weight, operating hours and angle of incline.
Nature of Material to be Conveyed
The abrasiveness of the conveyed material will have a significant effect on the wear rates of the conveyor. Sewage sludge cakes can vary greatly between sites although very abrasive sludge can normally be identified due to the effect that they would have on other equipment. For example an abrasive sludge will reduce the life of the scroll in a centrifuge and the rotor / stator in a progressive cavity pump. There are steps that can be taken to improve the wear rates where it is known that the conveyed material is abrasive such as fitting a different grade of liner. However this selection has to be made carefully as a more wear resistant liner will increase the wear rate on the spiral.
[[{"type":"media","view_mode":"media_original","fid":"2381","attributes":{"alt":"","class":"media-image","height":"746","typeof":"foaf:Image","width":"2006"}}]]
* Maximum Capacity is for horizontal applications only and can't be coincident with maximum length (Based on 20 RPM for sludge). Higher capacities may be achieved with higher RPM.
** Maximum length is for horizontal applications only and can't be coincident with maximum capacity.
Trough Size
Primarily this is determined by the required volumetric throughput or maximum object size. Although the angle of elevation will have an effect on the size and design (with an octagonal section trough required for angles above 30O and considered for angles above 25O).
[[{"type":"media","view_mode":"media_original","fid":"2374","attributes":{"alt":"","class":"media-image","height":"646","style":"font-size: 13.008px;","typeof":"foaf:Image","width":"884"}}]]
For Inclined conveyors adjust the capacity for trough selection by
Capacityadjusted = Capacityhorizontal x (1 + Angle of incline/60)
Motor Power and Speed
The primary factor to consider when selecting the motor speed is achieving the required throughput at the lowest possible speed. However this approach does tend to increase capital costs. For any given throughput, length of conveyor and angle of elevation there is a minimum required power. As the rotational speed is reduced, torque increases. This increase in torque results in an increase in the gearbox frame size. It would be possible to increase the speed, achieve the same throughput (by reducing the amount the trough was filled) and due to the lower torque a smaller gearbox could be used. Again this reduces capital cost but may increases whole life costs due to the increased wear rates.
Motor power and gearbox RPM
This is determined by the required length and throughput m3/hr (ft3/hr).
[[{"type":"media","view_mode":"media_original","fid":"2373","attributes":{"alt":"","class":"media-image","height":"532","typeof":"foaf:Image","width":"797"}}]]
[[{"type":"media","view_mode":"media_original","fid":"2371","attributes":{"alt":"","class":"media-image","height":"532","style":"font-size: 13.008px; font-weight: normal;","typeof":"foaf:Image","width":"797"}}]]
For Inclined conveyors adjust power requirement by:
Powerinclined = Powerhorizontal x (1 + Angle of incline/45)
Spiral Diameter, Pitch and Model
The spiral diameter and pitch are determined by the required throughput, angle of elevation and nature of the material. While these are not infinitely variable, SPIRAC have a very wide range of diameter and pitch combinations to suit many applications and capacities. The nature of the shaftless conveyors is such that one trough diameter is not limited to a single spiral diameter, there may be small variances in diameters of spirals for a given trough size. SPIRAC always aim for a relatively low speed of rotation to ensure low wear rates. Although it is often possible to use a smaller trough diameter and achieve the required throughput by increasing the speed of rotation the saving in capital cost is negated and may increase the whole life cost. The design of the spiral is also influenced by the angle of elevation.
The model of the spiral is determined by the requirement for an insert and also the required strength of the spiral. The strength is the ability to withstand the torque applied to the spiral. We have software that allows us to specify exactly which model of spiral is required to be used for any particular output torque. Yet again, significant savings on capital cost can be achieved by running at higher speeds, lower torques but this will always result in a higher whole life cost due to increase wear rates. Consideration should be given to hopper feeds, or other circumstances which might require that a conveyor designed to operate at a certain % fill may periodically fill to 100% in an upset condition thereby requiring adequate torque and motor HP to clear the trough.
Speak to SPIRAC
A reliable materials handling system for WWTP starts with selecting the right equipment. To learn more about the range of available spirals and how to select them, talk to us.